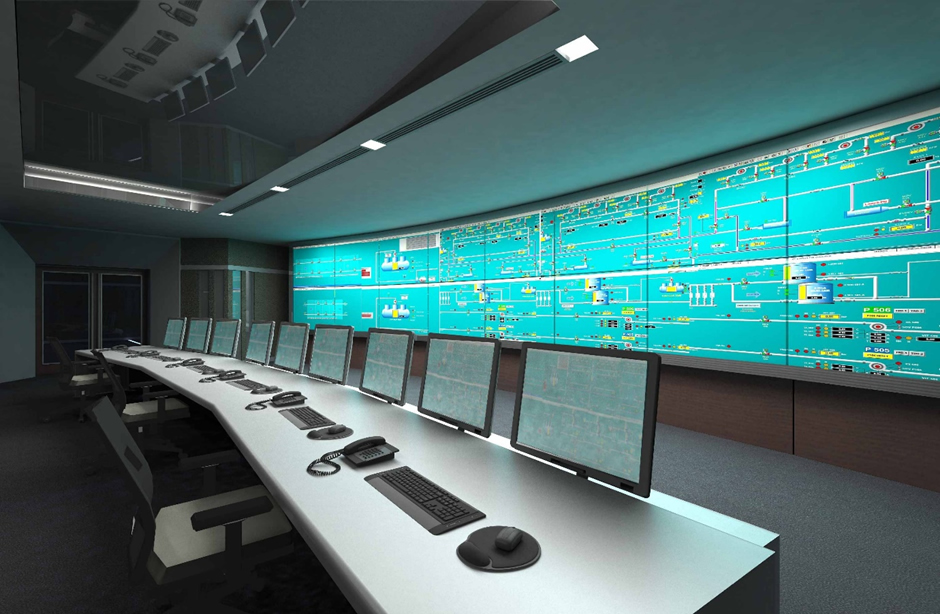 |
SCADA stands for Supervisory, Control and Data Acquisition and used for systems carrying out supervisory inspection and data acquisition towards processes. In this regard, it is frequently used together with the abbreviations, HMI (Human-Machine Interface) or MMI (Man-Machine Interface).
From a central control station up to a wide geographic region, SCADA systems in oil and gas fields, piping systems, water circuits, thermal and hydraulic power generation systems, transmission and distribution systems, advantageously allow the system operators, to reliably, safely and economically perform activities, such as to remotely control the valves, breakers, disconnectors, electric motors, electronic, electro-hydraulic and hydro-pneumatic valves, to change their set points, to display the alarms, to collect the measurement data, such as temperature, humidity, frequency, weight, number, element status.
It is inevitable to ensure the sustainability, quality and minimum cost in energy inputs under today’s circumstances where primary fuel reserves became scarce and the competition has dramatically increased, and to make investments to avoid a likely energy crisis. Therefore, cogeneration (combined heat-power generation) has become one of the leading energy management techniques today. Control of the plants constructed for this purpose can only be realized by using systems having a high level control philosophy as SCADA. In a combined cycle power plant, SCADA allows to continuously monitor the status of plant equipment, such as gas turbine, steam turbine, and heat recovery steam generator, water supply of the power plant, main distribution system and tanks, to collect data and to perform remote control activities.
By virtue of SCADA, which is an extensive and integrated data- based control and monitoring system, control of entire equipment in any plant or any operating, production planning, automated control and monitoring of all units, from environment control units to auxiliary systems, can be performed. SCADA control systems enable all control requirements of various operatings to be fulfilled in steps (layers). Integrated SCADA layers are described below. |
|
|
Operating Resource Management Layer
In this layer, where the resources of the operating required for production are planned, decisions supporting production and service policies are made and implemented. The data received from the lowest layer are evaluated in that layer of an integrated SCADA control system and strategies are developed, policies are defined and crucial decisions are made for the operating. |
Operating Management Layer
The cooperation between departments in the operating or plant is ensured at this level. Decisions, which are based on the strategies developed in the previous layer, are formed and the tasks are executed in the required order. |
 |
Process Control Layer
In the process control layer, it is aimed to ensure the synchronism between plants and equipment by performing monitoring and data collection functions. This layer commonly includes control devices and SCADA software within the central control room.
|
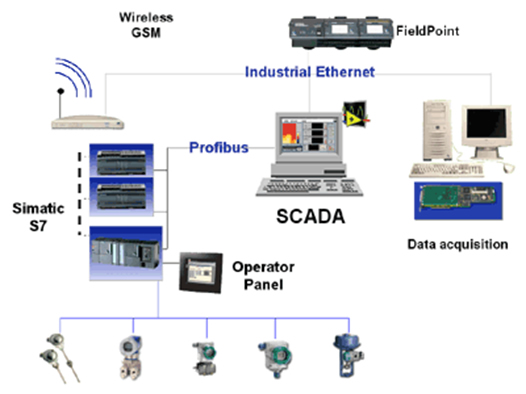 |
Operating Control Layer
The last layer of the automation pyramid can be defined as the layer, where the physical controls of the operating are performed. In this layer, mechanical and electronic devices are connected via interfaces and carry out operational functions. The control commands are transformed to electrical signals and mechanical movements, which ensures the proper working of the plant, while these transformed data are collected by means of electronic sensors. These data are transformed to electrical signals and transmitted to SCADA system. |
Advantages of SCADA:
- Continuous monitoring of the system
- Time and workforce saving,
- Ability to record and analyze the production data,
- Power monitoring and saving for the system,
- Avoidance of penalty cases (compensation etc.)
- Getting instantly acquainted on the field situation and immediate intervention,
- Register of system interventions,
- Locating the areas with fail risk,
- Instant acknowledgement on the system operation (status of the circuit breakers etc.) |
Application Area of SCADA
SCADA system has a wide application area. It has been used in many local and regional plants spreading over a large geographical area. The major application areas of SCADA system are as follows:
- Chemical Industry
- Natural Gas and Oil Pipelines
- Petro-chemical Industry
- Electricity Production and Transmission Systems
- Electricity Distribution Plants
- Water Collecting, Treatment and Distribution Plants,
- Air Pollution Control
- Cement Industry
- Building Automation
- Process Units |
SCADA systems should make possible:
to monitor the operating by means of mimics defined by the operator and objects to be used in the mimic screen (level, temperature, pressure, numerical signals, valve and motor status, system state etc.)
to enter the recipes via recipe screens and to acknowledge the operators on the processed recipes.
to input parameters required for the system via parameter screens (set point, high and low alarm limits etc.),
to enter and monitor the PID parameters,
to keep historic and real-time track of operational data,
to receive instant and periodical reports (production, recipe, inventory etc.),
to make manual interventions to the automated systems via SCADA screens,
to display alarms and events, to send to the printer and/or to save in the database.
High level quality control, e.g. statistical process control (SPC) support. |